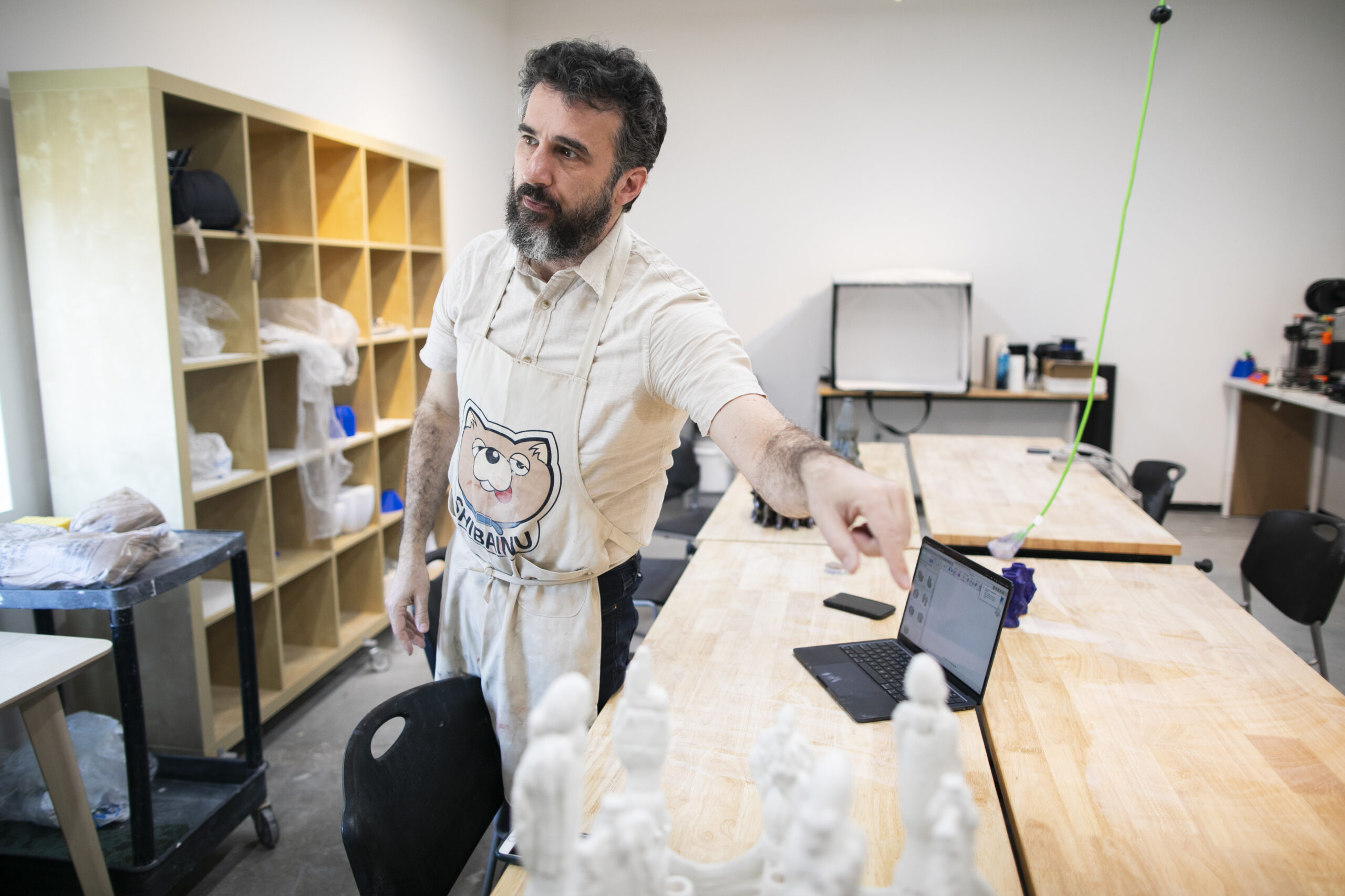
Visiting artist Nicolas Touron demonstrates the new 3D clay printer in Harvard’s Allston ceramics studio. He starts by creating a design on a computer.
Photos and video by Stephanie Mitchell/Harvard Staff Photographer
Merging sculpture, technology
New 3D clay printer helping shape the future of art in Ceramics Program
Ceramic artist Nicolas Touron kept a watchful eye on the nozzle of the machine as it circled the ware board, depositing a long noodle of clay. As coil layered upon coil and the walls of the abstract sculpture grew higher, Touron used a steady hand to add pieces of clay for stabilization, and a wet paintbrush to remove residue from the nozzle’s tip.
It was a Friday afternoon in Harvard’s Allston ceramics studio, and Touron, a visiting artist in residence with the Ceramics Program, Office for the Arts, had been building his latest piece using the program’s new 3D clay printer since 8 a.m. Starting next semester, the device will be used in courses and offer a new way for students in art, design, and engineering to work with clay.
“It’s really a process where you involve yourself in the machine if you want something interesting,” Touron said. “It’s partly like working with the [potter’s] wheel. If you don’t touch the machine, if you don’t understand the machine, you’re never going to have a good result.”
Kathy King, the director of Harvard’s Ceramics Program, is eager to provide the printer as a resource for artists who otherwise might not be able to access the technology. The LUTUM v4.6 was acquired this fall with the help of a grant from the Boger Family Foundation.
“I was really excited to just be able to start a conversation with people who may never ever try this machine but can be able to experience it as another option,” she said. “Another tool in the tool belt, in a way.”
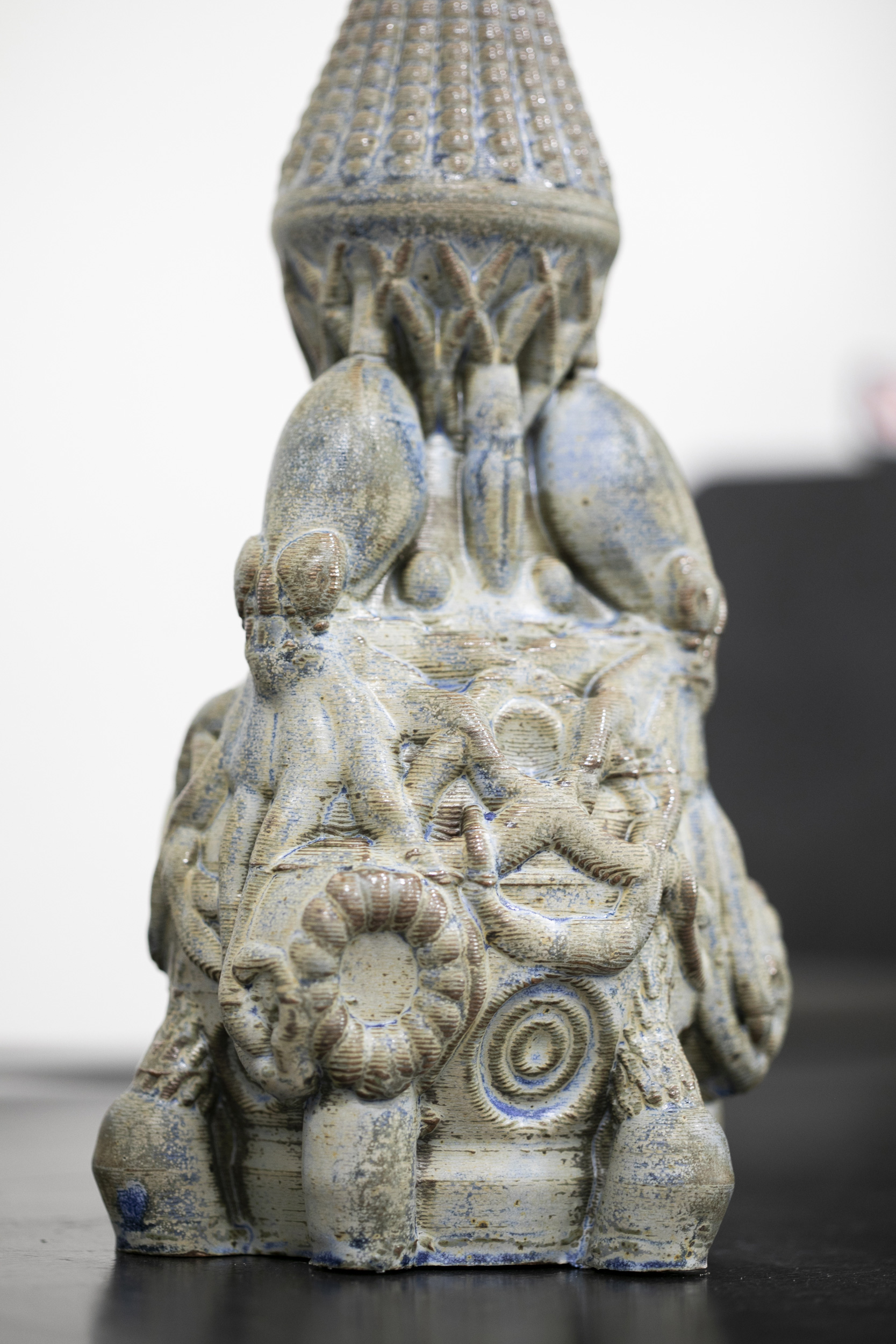
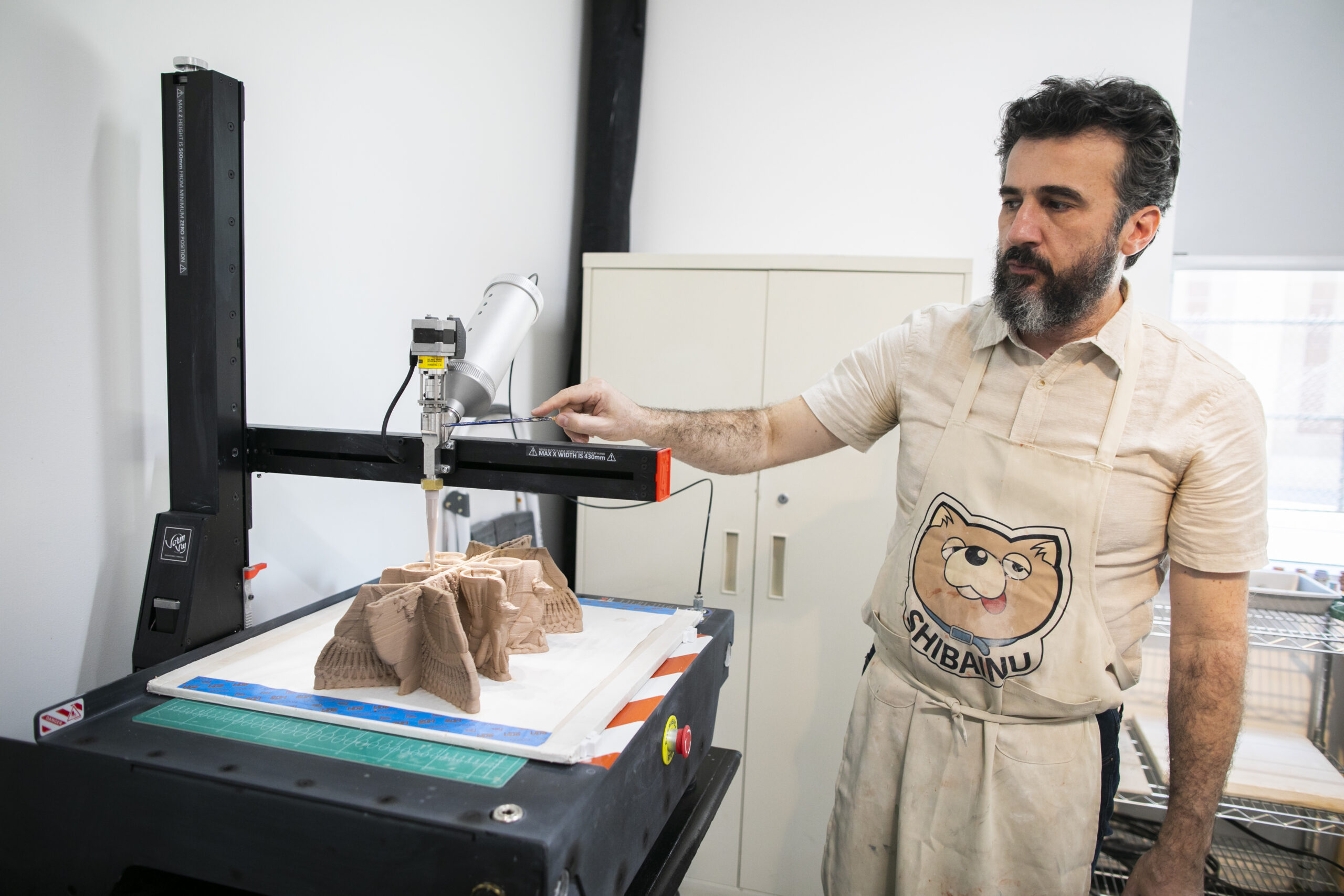
Detail of artwork created using the printer; Touron guides the machine.
While 3D clay printing has been used by designers and engineers for years — Harvard’s Graduate School of Design prints clay with a robot — it’s still a fairly new tool for artists. One benefit is it allows artists to make multiple prototypes of their sculptures or print smaller pieces to be combined later.
Touron says the process begins on a computer, where a software program allows an artist to create a design. A slicer program then converts it to 3D printing instructions.
Then the machine’s extruder — which resembles a tattoo gun — gets loaded with a cylindrical cartridge of clay, which is forced out in a thin line with pressure from an air compressor. After the device executes the design, the sculpture is ready for drying, glazing, and firing.
Touron said he likes viewing his ideas in 3D on the computer before starting with clay.
“For any kind of creative process, it’s amazingly efficient,” Touron said. “A sketch only gives you an idea, and it’s still a flat work. Here you can literally do your final work and decide if you want to proceed with making it.”
Although the technology is new, the coil technique is ancient. Coil pots were among the first clay vessels made by early civilizations around the globe.
“A sketch only gives you an idea, and it’s still a flat work. Here you can literally do your final work and decide if you want to proceed with making it.”
Today, 3D clay printers can be used to make sturdier replicas of ancient pottery pieces for educational purposes. The Ceramics Program has worked with the Harvard Art Museums before to recreate pieces from their collection by hand, and King is excited for what the new machine could bring to future collaborations.
Although conversations about new technology in art — most recently around AI — raise concerns about technology replacing artists, King says there’s nothing to fear here, at least for now. Clay printing still relies heavily on artists’ knowledge of the material, King said. For example, the machine can’t tell whether it is building a design that is too top-heavy to stand.
“I don’t think that there’s anything about this situation that we’re asking to replace anything,” King said. “This is to add another way of thinking, another way of seeing, another way of combining this method with ceramic art in general.”
If an error does happen, such as a clay cartridge running out while Touron is away getting a cup of coffee, he can’t back up the machine to fix the mistake. That’s why he stays vigilant.
“Anything could happen during the process because with organic matter, nothing is guaranteed,” he said.
Touron, who divides his time between Cambridge and New York City, led an introduction to clay printing workshop in March for a group who included students from the Graduate School of Design and staff from the School of Engineering and Applied Sciences, as well as local community members.
King said she is looking forward to incorporating the printer into more courses next school year.
“I’m hoping after a few of these, we’ll find some people who are ready to take on booking time with the machine, and working with some of our staff whom Nicolas has trained to be able to start printing on their own,” she said.